All laboratory personnel should be aware of and know what personal protective equipment (PPE) they should wear while performing various tasks in the histology laboratory. Employers are responsible for educating laboratory personnel about what hazardous chemicals they might handle, how to handle them safely and what specific protective equipment to wear for each and every task that is performed in the laboratory.
Employers must make use of engineering controls to help protect workers as well. In addition to the usual heating and cooling system of the work area, the histology laboratory should also have workstations that are vented to the outside, or make use of filters if vented back to the inside air.
Usually, there is at least one chemical fume hood located in the laboratory vented to the outside. Employees can use this space to pour off flammable/noxious chemicals, coverslip, or perform special stains that may generate hazardous fumes (i.e. mixing hydrochloric acid with potassium ferrocyanide to make the working solution of the Gomori’s stain for iron).
Performing the surgical grossing of specimens is one task that requires both full PPE and a ventilated work station. Laboratory employees must be protected against formaldehyde fumes and blood borne pathogens. Most pathology laboratories make use of units referred to as “grossing stations”. The most common grossing station is made of stainless steel which comprises the work surface, sides and front. This accommodates ease of cleaning and disinfection. Plumbing and a sink may be included for applications where large specimens (i.e. whole organs, limbs, etc.) are received. Strong lighting is required as well. Generally, a grossing station has a series of small exhaust fans (usually four) situated at the back of the work surface. Since formaldehyde is heavier than air (i.e. vapor pressure = 1.1), these fans pull the formaldehyde vapors into the back of the station, where they are collected into one vertically rising duct. The vapors are propelled along the inside of the duct with extra fans to move the vapors up the ductwork, to the outside of the building. An important regulation is that the exhaust duct on the roof of the building must not be anywhere near any intake vents for the building ventilation. Figure 1 shows an example of such a grossing station.
Another grossing station uses side and downdraft principles to manage heavy formaldehyde fumes. Figure 2 shows how the intake fans pull the fumes sideways, and move then downward. Once propelled downward, the fumes can go through a filter system to remove the hazardous fumes. This clean air can now be moved back into the laboratory. Clearly, the filters must be changed on a regular basis, according to the manufacturer’s recommendations. It is important to select the exact grossing station configuration that will work the best for your laboratory.
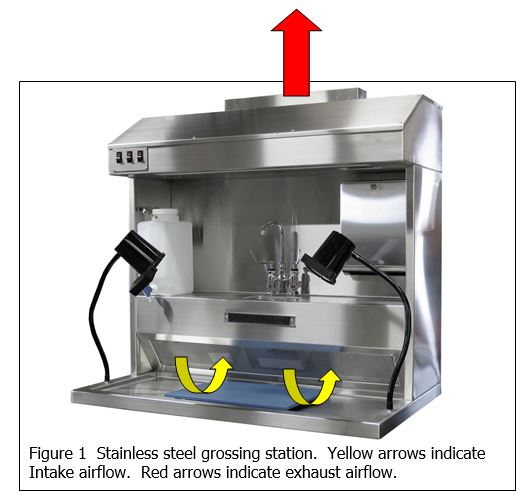
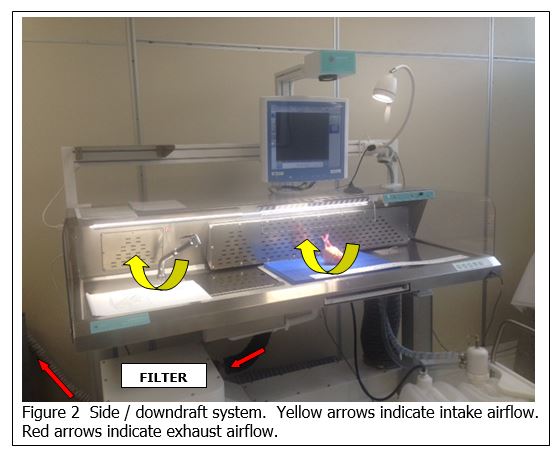
[Author’s note: Please be aware that OSHA’s regulatory standard 29 CFR Part 1910 describes exactly what employers and employees need to know with regard to Personal Protective Equipment (PPE), including mechanical controls. The entire standard can be found on the OSHA website. The following bullet points are taken from 29 CFR 1910.132 for your information, as an addendum to this article.]
29 CFR 1910.132 General Requirements
Application. Protective equipment, including personal protective equipment for eyes, face, head, and extremities, protective clothing, respiratory devices, and protective shields and barriers, shall be provided, used, and maintained in a sanitary and reliable condition wherever it is necessary by reason of hazards of processes or environment, chemical hazards, radiological hazards, or mechanical irritants encountered in a manner capable of causing injury or impairment in the function of any part of the body through absorption, inhalation or physical contact.
Design. All personal protective equipment shall be of safe design and construction for the work to be performed.
Select PPE that properly fits each affected employee
The employer shall verify that the required workplace hazard assessment has been performed through a written certification that identifies the workplace evaluated; the person certifying that the evaluation has been performed; the date(s) of the hazard assessment; and, which identifies the document as a certification of hazard assessment.
1910.132(e)
Defective and damaged equipment. Defective or damaged personal protective equipment shall not be used.
REFERENCES:
- Theory and Practice of Histological Techniques. JD Bancroft, A Stevens ed. Churchill Livingstone, NY. Fourth edition. 1996
- Theory and Practice of Histotechnology. DC Sheehan, BB Hrapchak. CV Mosby Company, St. Louis. First edition. 1980.
- Dermatopathology Laboratory Techniques. CM Chapman, I Dimenstein. 2016. Amazon.com
- Dapson and Dapson. Hazardous Materials in the Histopathology Laboratory. Anatech Ltd.
Your participation with comments and questions are much appreciated. They may just help other histotechs.